Up or down – where is the additive manufacturing industry heading? Impressions from Formnext 2023
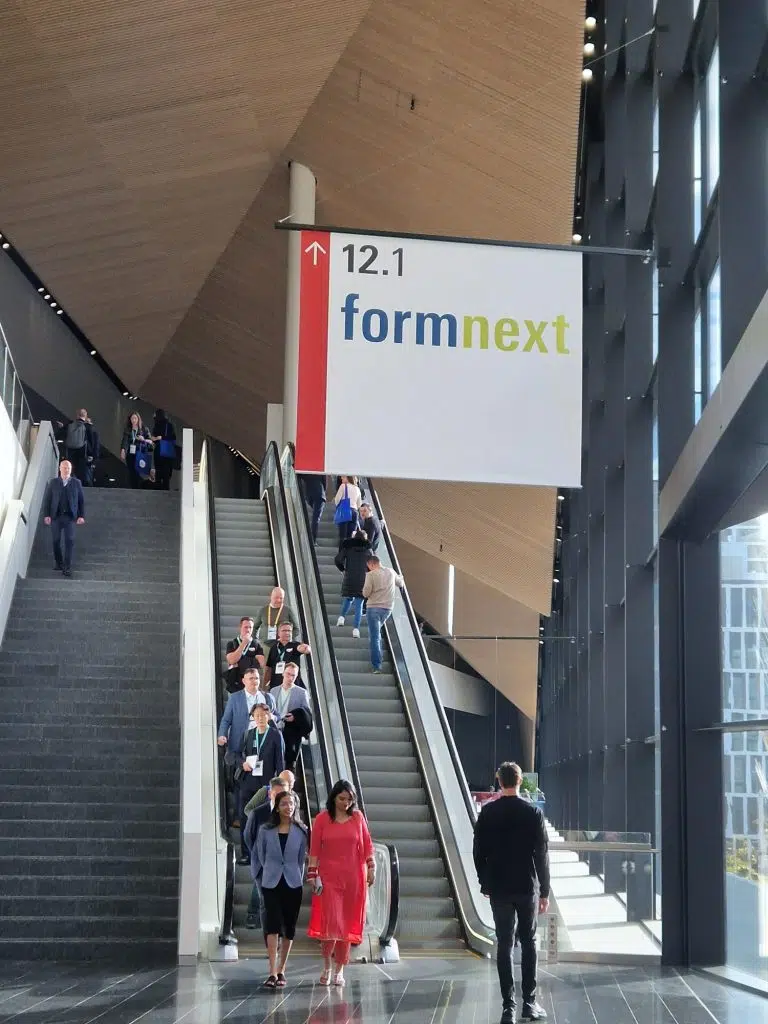
Formnext is an annual highlight for the additive manufacturing community. The 9th Formnext took place in Frankfurt on Nov 7-10, 2023, with 859 exhibitors (up from 802 in 2022). PAC took the opportunity to talk to leading vendors and start-ups in the additive manufacturing industry. Here are our key findings:
Formnext 2023 marks the end of the 3D-printing hype and shows a maturing industry
The fair did its best to keep the enthusiasm around the topic going, but reality became increasingly obvious. Additive manufacturing certainly remains a growth market, but that market is much smaller, with slower growth rates than initially expected. Recent mergers and acquisitions this year have painted a clear picture of market consolidation. We were under the clear impression that the hype was over and additive manufacturing was maturing. It is no longer considered as the future of manufacturing in general, but rather as a niche market for very specific purposes. In addition, there were three omnipresent topics at the fair, in our view – driving production process automation forward, and reducing production and material-related complexity for companies.
Driving production process automation forward
Siemens showcased solutions for the complete value chain, from planning through implementing a modular factory to operating it. One example in this context was the use of visual quality inspection based on Siemens Industrial Edge to optimize operations in the post-processing space.
Driving production process automation was not just a topic for large vendors at the show. Smaller vendors like PRINT&GO also presented interesting demos of 3D printers in combination with robots for loading and unloading 3D-printed parts and workflow software to enable autonomous production. What level of automation does a company actually need for its specific applications and business cases, though? After all, the complexity of the journey towards autonomous production should not be underestimated. For this purpose, Siemens, DyeMansion, BASF Forward AM, EOS, and HP introduced the Additive Manufacturing Navigator (AM Navigator) at this year’s Formnext. With this model, companies can refine their current status and their future target into 5 levels. The model is quite similar to the five levels of autonomous driving; it ranges from level 1, “basic”, to level 5, “autonomous”. The status quo of additive manufacturing can be analyzed by doing a Maturity Check for each company, following the structure of the framework. However, most companies are still in the early stages of this journey. Dr. Karsten Heuser, Vice President Additive Manufacturing at Siemens, confirms that even the most advanced 3D printing service providers have only reached level 3 so far.
Reducing production complexity for companies with limited experience in 3D printing
Companies still need a lot of support with creating 3D-printed parts according to their specific requirements. We observe different approaches in the market to support them. One is to offer a broad range of services that support clients in all aspects. This often starts with consulting, engineering, and manufacturing services but can also include providing software and integration services when clients want to establish their own 3D printing capabilities. Materialise is one good example in this context, with a lot of experience. The company offers a broad range of software, manufacturing services, and consultancy services for additive manufacturing for different industries, such as healthcare, automotive, aerospace, eyewear, art and design, wearables, and consumer goods. Another approach is a service from Schubert Additive Solutions, called PARTBOX, which allows user companies to send CAD files to an experienced engineering services provider to prepare the production job for a 3D printer and send it back to the user company for on-site production. According to Schubert, this can reduce the lead time from 10 to just 1 day. Schubert even offers to take over maintenance of the 3D printers at customers’ premises. This minimizes the complexity for user companies. Another approach is linked to virtual training and support. Toolcraft, for example, offers AMbitious, a virtual VR training solution for powder bed-based additive manufacturing in metal, and a maintenance app.
Tools to overcome material-related complexity
Materials are playing an increasingly significant role in additive manufacturing. The acquisition of the additive manufacturing materials business of Covestro by Stratasys in 2023 underscores this trend. At Formnext, for example, BASF showcased a broad portfolio of 3D printing materials, including the growing availability of sustainable printing materials. In response to the growing number of available printing materials for different purposes, we observe a growing number of tools to help clients survive in this jungle. Replique, the provider of a decentralized 3D printing platform, announced the launch of an open materials database for 3D printing at Formnext. The initial database will contain around 200 materials and can be accessed via the web by February 2024. The plan is for the database to grow quickly to more than 1,000 materials during 2024. 3YOURMIND introduced an updated materials database, offering software that is compatible with 1,200 materials and supports seven industrial AM technologies. Castor’s cloud-based or on-premises software technically and economically analyzes parts in the existing discrete manufacturing product design and identifies those that are suitable for additive manufacturing. The software also evaluates what materials and technologies are the most appropriate for the part in question. When a part is identified as a candidate for additive manufacturing, the software then calculates the financial break-even point of additive manufacturing versus traditional manufacturing. With the EOS Carbon Calculator, EOS offers a tool that enables AM users to understand the impact of the production process and the selection of different materials on the end product’s carbon footprint.